Types of Aircraft Construction
항공기 fuselage의 구조는 초기의 wood truss structure에서 monocoque shell structure로, 그리고 현재의 semimonocoque shell structure로 발전하였다.
Truss Structure
truss structure의 주요 단점은 유선형 모양이 없다는 것이다. 여기서는 가새를 대서 받치는 구조를 형성하기 위해 longerons가 적소에 용접된다. 수직/수평 지주가 longerons에 용접되어 정사각형, 혹은 직사각형 모양을 만든다. 모든 방향으로부터 발생할 수 있는 응력에 저항하려면 추가적인 지주가 필요하다. fuselage의 모양을 만들기 위해, 그리고 덮개를 지지하기 위해 stingers와 bulkheads(혹은 formers)가 추가된다.
기술이 발전함에 따라 항공기 설계자들은 비행기를 유선형으로 만들기 위해, 그리고 성능을 향상하기 위해 트러스 부재들을 둘러싸기 시작하였다. 초기에는 천으로 이루어졌으나 이는 결국 알루미늄과 같은 가벼운 금속으로 대체되었다. 경우에 따라 외부 표면이 비행 하중의 전부를, 혹은 대부분을 지지할 수 있다. 대부분의 현대 항공기는 monocoque, 혹은 semimonocoque로 알려진 이러한 응력 외피 구조(stressed skin structure)의 형태를 사용한다. [그림 3-14]
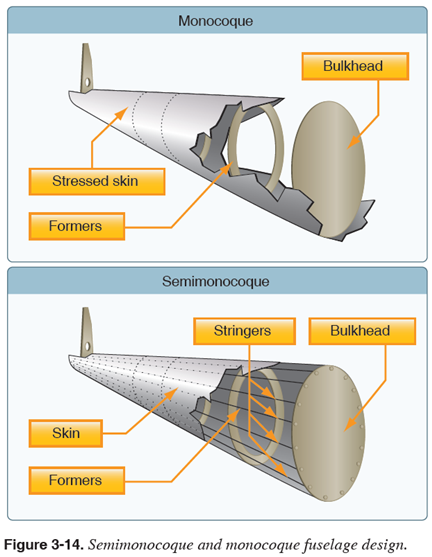
Monocoque
monocoque 구조는 거의 모든 하중을 지탱하기 위해 응력 외피를 사용한다. monocoque 구조는 매우 강하긴 하나 표면의 변형에 대한 내성이 높지는 않다. 예를 들어 알루미늄 음료 캔의 끝부분은 상당한 힘을 지지한다. 그러나 캔의 옆면이 하중을 지지다가 약간 변형될 경우 이는 쉽게 무너진다.
대부분의 비틀림 및 휨 응력은 외부 표면에 의해 견뎌진다. 따라서 내부 버팀대의 필요성이 사라짐에 따라 무게가 절약되고 공간이 극대화되었다. monocoque 구조는 초기 항공 산업에서 사용되었지만 이와 연관된 복잡성 때문에 수십 년 동안 다시 나타나지 않았다.
Semimonocoque
semimonocoque는 하부 구조를 부분적으로 사용한다. 하부 구조는 비행기의 표면과 부착된다. 하부 구조(bulkheads 및/혹은 formers, 그리고 stringers로 구성된)가 fuselage의 휨 응력을 일부 흡수함으로써 응력 외피를 보강한다. fuselage의 주요 부분에는 wing attachment points와 firewall이 포함된다. 단발 엔진 비행기에서 엔진은 일반적으로 fuselage의 앞부분에 부착된다. 엔진의 뒷부분과 조종실(혹은 객실) 사이에는 불연성 칸막이가 있다. 이는 우발적 엔진 화재로부터 조종사와 승객을 보호하기 위한 목적이다. 이러한 칸막이를 방화벽이라 부른다. 이는 내열성 물질(예를 들어 스테인리스강)로 만들어진다. 그러나 최근의 구조 공정에는 복합재가 통합되거나, 혹은 항공기 전체가 복합재로만 이루어진다.
Composite Construction
복합재는 광범위한 용어이다. 이는 섬유 유리, 탄소 섬유 천, 케블라 섬유 천, 그리고 이들의 모든 혼합물과 같은 물질을 의미할 수 있다. 복합재 구조는 두 가지 이점을 제공한다: 매우 매끄러운 표면, 그리고 복잡한 곡선이나 유선형 구조를 쉽게 형성할 수 있는 능력. [그림 3-15]
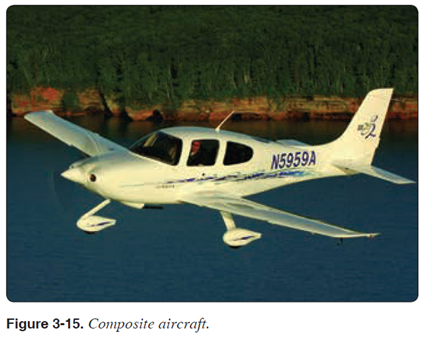
Composite Materials in Aircraft
복합재는 fiber-reinforced matrix 시스템이다. matrix는 섬유들을 함께 고정하는데 사용되는 접착제이다. 이것이 경화되면 부품에 형태를 제공하며 섬유가 대부분의 하중을 지탱한다. 다양한 유형의 섬유/matrix 시스템이 있다.
항공기에서 가장 일반적인 matrix는 열경화성 플라스틱의 일종인 에폭시 수지이다. 에폭시는 다른 선택지(예를 들어 폴리에스테르 수지)에 비해 강하며 고온 특성이 좋다. 구조적 특성, 경화 시간 및 온도, 그리고 비용이 광범위한 다양한 종류의 에폭시 수지를 사용할 수 있다.
항공기 구조에 사용되는 가장 일반적인 강화 섬유는 섬유 유리, 그리고 탄소 섬유이다. 섬유 유리는 인장 강도, 압축 강도, 그리고 내충격성이 좋다. 또한 취급하기 편리하며 비교적 저렴하여 쉽게 이용할 수 있다. 가장 큰 단점은 무게가 다소 무겁다. 또한 제대로 설계된 알루미늄 구조보다 더 가벼운 섬유 유리 구조를 만드는 것은 어렵다.
탄소 섬유는 일반적으로 섬유 유리보다 인장 강도와 압축 강도가 더 강하다. 또한 휨 강도가 훨씬 높으며 섬유 유리보다 상당히 가볍다. 그러나 내충격성이 상대적으로 약하다(부서지기 쉬우며 날카로운 충격에 의해 산산조각 나는 경향이 있음). 이는 “toughened” epoxy resin 시스템을 통해 크게 개선될 수 있다. 탄소 섬유는 과거 섬유 유리보다 비쌌으나 현재는 가격이 떨어졌다. 제대로 설계된 탄소 섬유 구조는 알루미늄 구조보다 상당히 가벼울 수 있다.
Advantages of Composites
복합재 구조는 금속, 목재, 혹은 직물에 비해 몇 가지 장점을 제공한다. 장점들 중 가장 많이 언급되는 것은 경량화이다. 경량화가 항상 자동으로 따라오는 것은 아니다. 복합재로 항공기 구조를 만든다 하여 경량화가 보장되는 것은 아니다. 이는 구조, 그리고 사용되는 복합재의 유형에 따라 달라진다.
더 중요한 장점은 복합재로 만들어진 매우 매끄러운 곡선 모양의 공기역학적 구조가 항력을 줄여준다는 것이다. 항공기에서 복합재를 사용할 경우 항력이 감소하여 fixed landing gear를 가지고 있음에도 불구하고 높은 성능을 얻을 수 있다. 복합재는 또한 “스텔스” 항공기 설계의 레이더 신호를 감추는데 도움을 준다. 오늘날 복합재는 글라이더부터 신형 헬리콥터에 이르기까지 다양한 종류의 항공기에서 발견될 수 있다.
부식이 없는 것은 복합재의 세 번째 장점이다. 보잉은 787의 fuselage를 전부 복합재로 설계한다. 이는 이전의 여객기보다 더 높은 압력 차이, 그리고 높은 습도를 가질 수 있다. 엔지니어들은 더 이상 fuselage 표면의 숨겨진 부분(예를 들어 블랭킷 단열재의 뒷부분)에서 발생한 수분 응축, 그리고 이로 인한 부식에 대해 걱정하지 않는다. 이를 통해 항공사의 장기 유지보수 비용을 절감할 수 있다.
Disadvantages of Composites
복합재는 고유한 단점들을 가지고 있다. 그 중 가장 중요한 것은 손상에 대한 시각적 증거가 없다는 것이다. 복합재는 충격에 대해 다른 구조 물질들과는 다르게 반응하며 손상의 명확한 징후가 대부분 없다. 만약 자동차가 후진하다 알루미늄 동체에 부딪힐 경우 그 동체가 찌그러질 수도 있다. 만약 동체가 찌그러지지 않았다면 손상이 없는 것이다. 만약 동체가 찌그러졌다면 손상이 눈에 보이며 수리가 이루어진다.
복합재에 대한 낮은 에너지 충격(예를 들어 공구를 떨어뜨림)은 눈에 보이는 충격 징후를 표면에 남기지 않을 수 있다. 충격 부위 아래에서는 광범위한 박리(충격 부위로부터 원뿔 모양으로 퍼진)가 있을 수 있다. 구조 뒷면의 손상은 심각하고 광범위할 수 있지만 눈에 보이지 않을 수 있다. 충격이 있었다 생각될 경우 복합재에 익숙한 검사관으로부터 구조를 검사받아서 손상을 확인하는 것이 좋다. 섬유 유리 구조에서 희끄무레한 영역이 나타나는 것은 섬유 균열의 박리가 발생하였음을 암시하는 좋은 정보이다.
중간 정도의 에너지 충격(예를 들어 차량이 구조물로 후진할 경우)은 눈에 보일 정도의 국부적 찌그러짐을 표면에 발생시킨다. 손상 부위는 눈에 보이는 찌그러진 부분보다 더 크므로 수리가 필요하다. 높은 에너지 충격(예를 들어 비행 도중 조류 충돌, 혹은 우박)은 펑크, 그리고 심하게 손상된 구조로 이어진다. 중간 및 높은 에너지 충격에서는 손상이 눈에 보인다. 허나 낮은 에너지 충격은 감지하기 어렵다. [그림 3-16]

충격으로 인해 박리, 표면의 찌그러짐, 혹은 펑크가 발생하는 경우 수리가 필수적이다. 수리를 기다리는 동안 손상 부위를 덮어서 비로부터 보호해야 한다. 많은 복합재 부품들이 honeycomb core위의 얇은 층들로 구성되어 “sandwich” structure를 만든다. 이는 구조 강성에서 매우 우수하다. 허나 수분 침투가 쉬워서 나중에 추가적인 문제로 이어진다. 펑크 위에 “speed tape”를 붙이는 것은 물로부터 보호하는 좋은 방법이다. 허나 이는 구조적인 수리가 아니다. 손상을 덮기 위해 paste filler를 사용하는 것은 미용상의 목적에선 허용된다. 허나 이 또한 구조적인 수리가 아니다.
수지(resin)의 열 손상 가능성은 복합재를 사용할 때의 또 다른 단점이다. 많은 에폭시 수지가 화씨 150도 이상에서 약화되기 시작한다. 이 문제를 최소화하기 위해 복합재에 흰색 페인트를 사용하는 경우가 많다. 예를 들어 검정색으로 칠해진 날개의 아랫면은 덥고 화창한 날에 화씨 220도까지 뜨거워질 수 있다. 반면 흰색으로 칠해진 동일한 구조는 화씨 140도를 초과하는 경우가 거의 없다. 그 결과 복합재 항공기는 허용 가능한 페인트 색상에 대해 특정한 권장 사항을 제시하는 경우가 많다. 항공기를 다시 페인트칠 하는 경우 이러한 권장 사항을 따라야 한다. 화재로 인한 열 손상 또한 발생할 수 있다. 자그마한 브레이크 화재를 빠르게 소화하였다 하여도 날개 하부 표면, 복합재 착륙 기어, 혹은 wheel pants를 손상시킬 수 있다.
또한 화학적 페인트 제거액은 복합재에 매우 해로우므로 복합재에 사용해서는 안 된다. 복합재에서 페인트를 제거해야 하는 경우에는 오직 기계적 방법(예를 들어 grit blasting, 혹은 sanding)만을 사용할 수 있다. 많은 고가의 복합재 부품들이 페인트 제거액의 사용으로 인해 손상되었다. 이러한 손상은 일반적으로 복구될 수 없다.
Fluid Spills on Composites
일부 소유자들은 복합재 표면에 연료, 오일, 혹은 유압유를 쏟는 것을 우려한다. 에폭시 수지를 사용하는 현대의 복합재에서는 일반적으로 문제가 없다. 이러한 것들을 쏟았을 때 페인트가 손상되지 않았다면 이는 보통 복합재에 손상을 주지 않는다. 예를 들어 일부 항공기는 섬유 유리로 된 연료 탱크를 사용하여 연료가 복합재 표면에 직접 닿는다. 만약 섬유 유리 구조가 좀 더 저렴한 형식의 폴리에스테르 수지로 만들어졌다면 에탄올이 혼합된 auto gas를 사용할 때 문제가 발생할 수 있다. 폴리에스테르 수지와 에폭시 수지가 더 비싼 형식일 경우 이는 auto gas, 100 octane avigation gas, 그리고 jet fuel과 함께 사용될 수 있다.
Lightning Strike Protection
낙뢰 방지는 항공기 설계에서 중요한 고려 사항이다. 항공기가 번개에 맞을 경우 매우 많은 양의 에너지가 구조물로 전달된다. 범용 항공 항공기나 대형 여객기나 낙뢰 방지의 기본 원리는 동일하다. 항공기의 크기와 상관없이 낙뢰로 인한 에너지가 넓은 표면적으로 분산되어야 한다. 이는 평방인치 당 암페어를 무해한 수준으로 낮추기 위함이다.
낙뢰가 알루미늄 비행기에 부딪히면 전기 에너지가 알루미늄 구조물을 통해 쉽게 전달된다. 문제는 에너지가 안전하게 바깥으로 전도되기 전까지 항법 장비, 연료 시스템 등등을 에너지로부터 보호하는 것이다. 항공기의 외부 표면은 저항이 가장 적은 경로이다.
섬유 유리는 우수한 전기 절연체이다. 반면 탄소 섬유는 전기를 전도하긴 하나 알루미늄만큼은 아니다. 따라서 복합재 표면의 바깥층에 추가적인 전기 전도가 필요하다. 이는 일반적으로 미세한 금속 망(metal mesh)을 표면에 접합함으로써 수행된다. 알루미늄 망(aluminum mesh)과 구리 망(copper mesh)이 가장 일반적인 두 가지 유형이다. 알루미늄은 섬유 유리에서, 그리고 구리는 탄소 섬유에서 사용된다.
내부 무선 안테나가 있는 복합재 항공기의 경우 안테나 영역의 lightning strike mesh에 창문이 있어야 한다. 내부 무선 안테나는 섬유 유리 복합재에서 찾을 수 있다. 왜냐하면 섬유 유리는 라디오 주파수를 통과시키지만 탄소 섬유는 그렇지 않기 때문이다.
'PHAK(2023) > 3: Aircraft Construction' 카테고리의 다른 글
(3) Lift and Basic Aerodynamics (0) | 2023.05.07 |
---|---|
(4) Major Components (0) | 2023.05.07 |
(5) Subcomponents (0) | 2023.05.07 |
(7) Instrumentation - Moving into the Future (0) | 2023.05.07 |
(8) Global Positioning System (0) | 2023.05.07 |